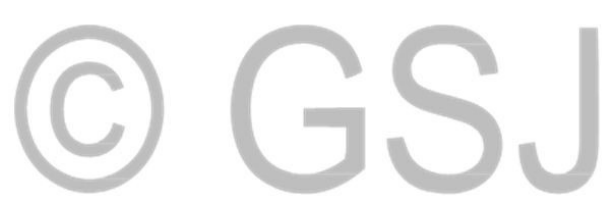
2
1. INTRODUCTION
Kaolin is a unique industrial mineral that remains chemically inert over a wide pH range and offers excellent
coverage when used as a pigment in coated films. It is widely used as filler in the plastics industries due to
its inert chemical nature and its unique size, shape and structure. Most of the alternative wall making
materials used in the tropical countries was making from stabilized earth blocks, which lose their fertile
clay soil. Hence, it is better to replace this fertile stabilized earth block with loosen non fertile low graded
kaolin clay blocks that can be found abundantly in most of the high land and low land area of Ethiopia
(Haile Michael, et.al, 1998).
Ethiopia is known in the world as the museum of Ethnography, Archeology and Anthropology; for it is
residence of path of civilization and the cradle of humankind. Therefore, the eminence of the country goes
far in calling the attention of the world intellectuals on various fields including Architects, Civil Engineers
and Geoscientists due to having historical building monument (Mines, M.O, 2011).
Hollow concrete blocks produced in the major local sites in Ethiopia is from different composite materials
like fine gravel of different size (00 and 01 mm), Cement, Sand, Red Ash, Pumice, River dune sand, Scoria
and water in predetermined proportions. The blocks used in the world have similar overall dimensions
whereas, some have two hollow cores and the other might be three. Block dimensions vary, but in general,
the length and depth are around 400mm and 190mm respectively. The blocks manufactured in plants using
the “dry cast” process using a mix of kaolin, sand, fine gravel, Portland cement, Bagasse Ash, sawdust and
a limited amount of water in predetermined proportions. The concrete mix was feeding into molds, using
pressure and vibration for compaction, after which the block exits the mould (Svetlana Brzev and P.Eng
2012).
The successful application of kaolin clay and agro waste in building materials would not only serve as a
cost-effective alternative to the current disposal method, but also offer a large potential market for its
utilization in alternate building materials. At present, Ethiopia had little experience in the utilization of
different construction materials. The conventional materials are produced from mortar, gypsum, clay,
limestone and others materials, excavated from the ground. On the other hand, the demand of these building
materials was not compatible with the supply. This had an impact on the rising of cost of cement and other
construction materials (Abebe Dinku and Asnake 2003).
It was believed that there are numerous sources of kaolin clay in Ethiopia and currently exploration
activities carried out throughout the country. There are so many resources not even partially utilize its
potential in order to contribute to the construction industry (Haile Michael and Mengistu 2003). Hence, the
GSJ: Volume 9, Issue 8, August 2021
ISSN 2320-9186
GSJ© 2021
www.globalscientificjournal.com